Materialien, die mehr können
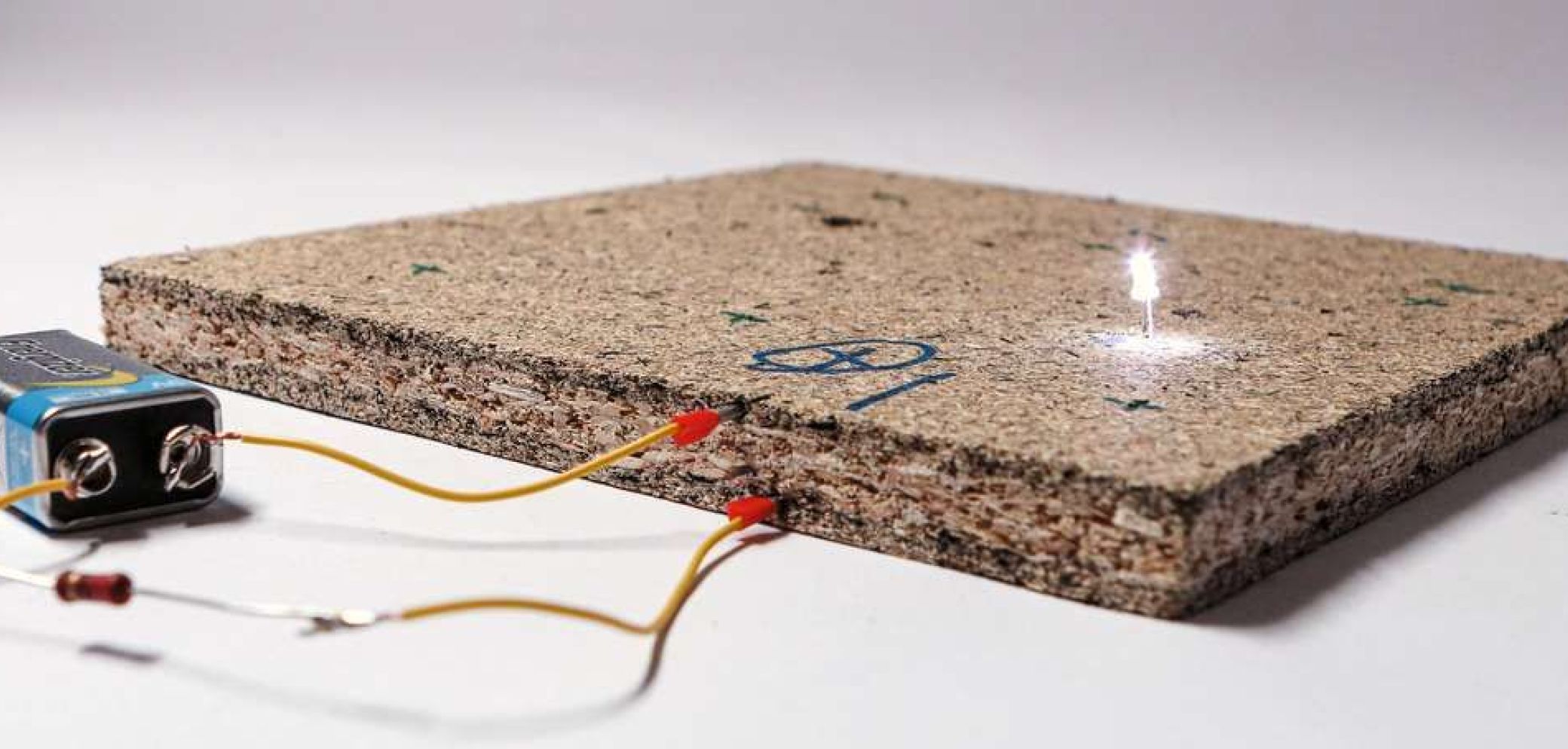
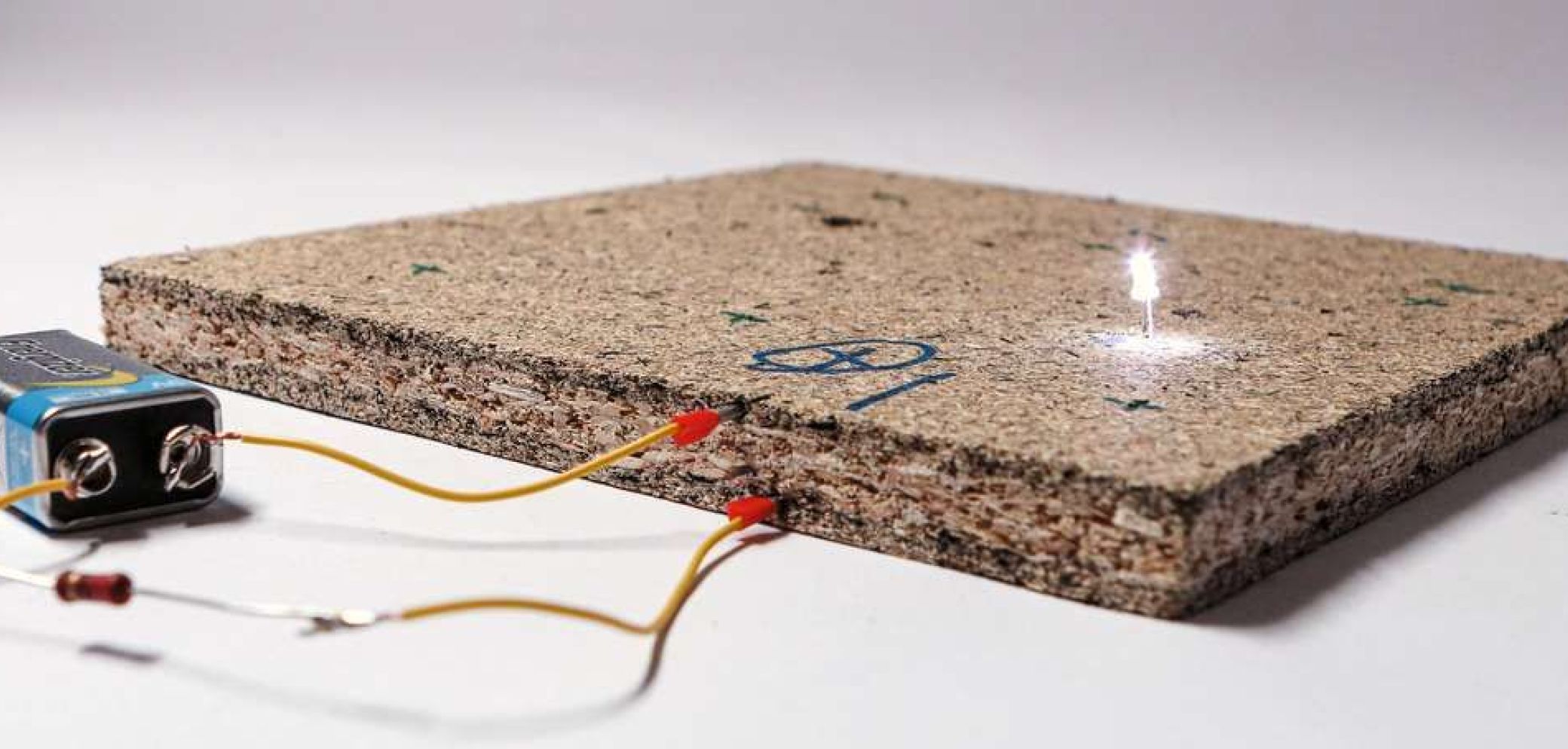
Diese Spanplatte hat es in sich: Dank Kohlenstofffasern leitet sie Strom in die Deckschicht. Bild: Berner Fachhochschule
Diese Spanplatte hat es in sich: Dank Kohlenstofffasern leitet sie Strom in die Deckschicht. Bild: Berner Fachhochschule
Forschung. Der Schreiner hantiert täglich mit den unterschiedlichsten Werkstoffen. Deren Eigenschaften sind bis zu einem gewissen Grad vorgegeben. Doch die Materialien lassen sich im Labor verändern und anpassen. Ein Blick auf zwei Forschungsprojekte.
Damit das Publikum der Messe Holz 2019 Zugriff auf sämtliche Hintergrundinformationen, Hallenpläne und Messehighlights hat, werden die E-Paper Ausgaben 39, 40, 41 und 42 freigeschaltet. Diese SchreinerZeitungen im Digitalformat sind somit vorübergehend ohne Login und kostenlos abrufbar.
Das E-Paper ist über die Webseite epaper.schreinerzeitung.ch erreichbar. Für die Mobile-Geräte steht im Apple Store (für Apple-Geräte) oder im Google Play Store (für Android-Geräte) die SchreinerZeitungs-App zum kostenlosen Download bereit.
Das eine Holz ist hart, ein anderes eher weich, ein Werkstoff brennt wie Zunder, ein anderer gar nicht. Jedes Material hat seine guten und weniger guten Eigenschaften. Mit den meisten muss man sich als Schreiner wohl oder übel abfinden. Oder doch nicht? Im Labor lässt sich noch so manches aus den Werkstoffen herausholen, indem sie modifiziert oder mit zusätzlichen Stoffen angereichert werden. So bekommen zum Beispiel Spanplatten Zusatzfunktionen, oder weiche Hölzer können dichter und härter gemacht werden. Zwei aktuelle Forschungsprojekte zeigen, woran derzeit getüftelt wird.
Die kleine LED-Birne steckt mitten in der Spanplatte und leuchtet. Ein Kabel, welches zur Lichtquelle führt, ist weit und breit keines auszumachen. Auch in der Platte selbst verlaufen keine Drähte. Diese Spanplatte erhielt sozusagen ein Upgrade und kann nun etwas mehr: Sie selbst leitet den Strom durch sich hindurch. Ein interdisziplinäres Forscherteam an der Berner Fachhochschule in Biel (BFH) hat dieses innovative Beleuchtungskonzept für Wohnmöbel entwickelt. Dank dieser kabellosen Stromleitung durch die Trägerplatte hindurch können Leuchten hochflexibel positioniert werden. Das System schafft damit völlig neue Gestaltungsmöglichkeiten, und unschöne sowie aufwendige Kabelkanäle fallen gänzlich weg.
Das BFH-Forscherteam, welches sich aus Mitarbeitern der Departemente Architektur, Holz und Bau (BFH-AHB) sowie Technik und Informatik (BFH-TI) zusammensetzt, stellte sich die Frage, wie man Möbel intelligenter und mit zusätzlichen Funktionen ausstatten kann. Sie nahmen als Ausgangspunkt die wenig beachtete Grundstruktur von Spanplatten unter die Lupe. Diese werden heute industriell durch Verpressen einer mit Klebstoff angereicherten Matte aus Holzspänen hergestellt. Aufgebaut ist die Platte in drei Schichten: Zwei Deckschichten und dazwischen die etwas gröbere Mittelschicht. Mischt man nun den Spänen der beiden Deckschichten einen vergleichsweise geringen Anteil Kohlenstofffasern hinzu, entsteht eine Platte mit einer guten elektrischen Leitfähigkeit.
«Ein Vorteil ist, dass die Kohlenstofffasern auch in geringerer Qualität nichts von ihrer Leitfähigkeit einbüssen. Das erlaubt uns auch, mit recyceltem Kohlenstoff zu arbeiten, was sich auf den Preis der Platte positiv auswirkt», sagt Heiko Thömen, Leiter Kompetenzbereich Verbundwerkstoffe und Möbelentwicklung an der BFH, der sich dem Projekt der kabellosen Energieversorgung widmet. Den Platten wurden ungefähr zehn Prozent Kohlenstofffasern beigefügt, die Leitfähigkeit sei aber auch bei einem geringeren Anteil noch gegeben.
Damit der Niedervoltstrom durch das gesamte Möbel fliessen kann, muss bei der Konstruktion auf die Verbindungen zwischen den Seiten und den Böden geachtet werden. «Auf Gehrung zusammengefügte Seiten funktionieren bestens. In der Regel muss man sich aber mit speziell gestalteten Verbindungen weiterhelfen», erklärt Thömen. Auch müsse man darauf achten, dass man keinen – wenn auch ungefährlichen, so doch störenden – Kurzschluss im Möbel provoziere.
Die Einschraubfassung der LED-Leuchten musste vom Projektteam ebenfalls neu entwickelt werden. Mittlerweile konnte auch dieses Teil zum Patent angemeldet werden. Die Fassung ist überwiegend aus einem nicht leitenden Kunststoff gefertigt und hat einen Durchmesser von wenigen Millimetern. Durch Einschrauben der Fassung in ein einseitig vorgebohrtes Loch wird der Kontakt zwischen den beiden Metallenden der Fassung und den stromführenden Schichten der Spanplatte hergestellt: Der Stromkreis wird geschlossen und die LED leuchtet. Um eine LED-Birne zu platzieren, braucht es also lediglich eine Bohrmaschine. Wo gebohrt wird, spielt keine Rolle.
Der Strom für die Beleuchtung stammt von einem Netzteil, einer Batterie oder, im besten Fall, von einem Fotovoltaik-Element mit Solarzellen. Dieses Element kann an einer Seite des Möbels angebracht werden, wo es tagsüber einen Akku füllt. Um einen Kleiderschrank inwendig mit Licht auszuleuchten, reiche das vollkommen aus, erläutert Thömen. Schliesslich benötige man das Licht nur für kurze Zeit, bis die Kleider ausgewählt oder wieder versorgt sind.
Verschiedene Vertreter von Designmöbelfirmen hätten sich schon begeistert gezeigt, freut sich Thömen. Man ist aber auch mit den Grossen, zum Beispiel mit Ikea, im Gespräch. Mit dem schwedischen Riesen werden noch im Oktober erste Gespräche stattfinden. Doch bis ein Plattenhersteller eine solche Spanplatte im grossen Stil produziere, gäbe es noch ein paar Hürden zu nehmen. «Ich bin dennoch sehr zuversichtlich, dass dies zu schaffen ist», prognostiziert Thömen. Als nächster Schritt sei eine Machbarkeitsstudie geplant, die präzisieren soll, auf welchem Weg der Sprung in die Produktion zu schaffen sei. Bis Ende Jahr soll dies geklärt werden.
Ebenfalls in Biel, nur ein paar Räume weiter, kratzt ein Fingernagel mit viel Druck über Fichtenholz. Normalerweise würden nun gut ersichtliche Spuren im Holz zurückbleiben, doch an diesem Stück Holz gibt es nichts zu kratzen. Überhaupt, die Haptik dieses kleinen Stücks Tannenholz hat nicht mehr viel mit dem Original gemein. Es fühlt sich eher an wie Kunststoff. Die Oberfläche ist ganz glatt, als wäre sie auf Hochglanz poliert. Und doch, dieses Holz ist nach wie vor zu 100 Prozent Holz, ohne irgendwelche Zusatzstoffe.
Doch wie kommt es zu dieser Verwandlung? Die Antwort scheint ganz einfach: Das Holz wird verdichtet. Sprich, die Zellzwischenräume werden verkleinert, ohne dabei die Holzfasern zu verletzen. «Dieses Verfahren ist an sich nicht neu. Wir konnten es aber weiterentwickeln, dass es nun auch für Partner aus der Wirtschaft interessant wird», sagt Frédéric Pichelin, Leiter Institut für Werkstoffe und Holztechnologie an der Berner Fachhochschule in Biel.
Das Verfahren gleicht dem traditionellen Dampfbiegeverfahren. Dabei wird das Holz 140 Grad Celsius heissem Dampf ausgesetzt. Dieser durchdringt die Holzfasern schnell und gleichmässig, bis diese ihre Transformationstemperatur erreichen. Das heisst, das Holz verwandelt sich in einen zähflüssigen Zustand, ohne dass seine Struktur dabei beschädigt wird. Sobald dieser Punkt erreicht ist, wird das Holz gepresst.
Die Verdichtung erfolgt schrittweise, um Spannungen abzubauen. Wie dicht das Holz wird, kann selbst bestimmt werden. Zum Schluss wird das Holz noch einmal erhitzt, wobei es unempfindlicher gegenüber Feuchtigkeitsschwankungen gemacht wird. Bis der Verdichtungsprozess abgeschlossen ist, vergehen, je nach Enddichte, zwischen 20 Minuten und zwei Stunden.
«Es ist uns zum Beispiel möglich, ein Stück Weisstanne um 67 Prozent zu verdichten», erklärt Benoît Canoine, Wissenschaftlicher Mitarbeiter der BFH und Projektleiter dieser Studie. In Zahlen ausgedrückt heisst das, dass die Tanne, die vor der Modifizierung eine Dichte von 450 Kilogramm auf einen Kubikmeter aufwies, danach stolze 1350 Kilogramm pro Kubikmeter auf die Waage bringt. Im Vergleich: Tropisches Ebenholz wiegt zwischen 1000 und 1250 Kilogramm pro Kubikmeter. Mit dieser Verdichtung wird Holz in etwa so hart wie ein leichtes Aluminium.
Dieses Verdichtungsverfahren eröffnet heimischen Hölzern neue Möglichkeiten in der Verwendung. «Wir haben bereits einen Wirtschaftspartner an unserer Seite, der sich sehr für die Weiterentwicklung des Produkts einsetzt», sagt Canoine. Dabei handelt es sich um eine Zulieferfirma für die Uhrenindustrie. Man könne sich also denken, in welche Richtung die Entwicklung gehe. Unterstützt wird das Forschungsprojekt zudem von Innosuisse, der vom Bund finanzierten Agentur für Innovationsförderung. Ihre Aufgabe ist es, wissenschaftsbasierte Innovationen im Interesse der Wirtschaft voranzutreiben.
«Wir haben dieses Jahr damit begonnen, nur an der Oberfläche verdichtete heimische Hölzer für den Aussenbereich zu testen», ergänzt Pichelin weiter. Das mache die heimischen Hölzer noch spannender für Terrassenböden oder Gartenmöbel.
Bis dieses modifizierte Holz für den Schreiner erhältlich ist, braucht es noch etwas Geduld. Im Moment gehe es nicht nur darum, das Verhalten der verschiedenen Hölzer zu testen, sondern auch, um den Verdichtungsprozess und die Maschine selbst hinsichtlich Energie- und Kosteneffizienz zu optimieren.
«Wir können uns vorstellen, dass der Schreiner irgendwann seine eigene Verdichtungsanlage besitzt und so sein Holz für seine jeweiligen Verwendungszwecke anpassen kann. Auch ist es vielleicht irgendwann möglich, gleichzeitig zu biegen und zu verdichten. Dies würde wiederum neue Möglichkeiten eröffnen», blickt Canoine in die Zukunft. Sein Team rechnet damit, dass es erste Prototypen bereits Ende nächsten Jahres präsentieren kann.
Unter die zehn Besten des Innovationspreises 2019 kam auch Sonowood. Es wurde, ähnlich dem verdichteten Holz, als Ersatz von Tropenholz im Instrumentenbau entwickelt. Die Preisverleihung des Innovationspreises findet an der Eröffnungsfeier am 15. Oktober an der Messe Holz in Basel statt.
ids
Veröffentlichung: 03. Oktober 2019 / Ausgabe 40/2019
Linoleum. Bei Schreibtischen und Sekretären wird Linoleum aufgrund seiner angenehmen Haptik besonders gerne eingesetzt. Dank seiner natürlich antibakteriellen und pflegeleichten Eigenschaften macht das Material aber auch in der Küche eine gute Figur.
mehrDispersionsklebstoffe. Auch beim Weissleim wird das Thema Nachhaltigkeit immer wichtiger, und moderne Produkte punkten mit ökologischen Inhaltsstoffen. Grund genug für den Schreiner, die neusten Entwicklungen und Produkte zu kennen.
mehrPaidPost. Der erste Argolite Montage-Leitfaden ist da. Mit dessen Hilfe können Schreinerinnen und Schreiner individuelle Wandverkleidungen im Badezimmer spielend leicht realisieren.
mehr