Was gut fräst, will Weile haben
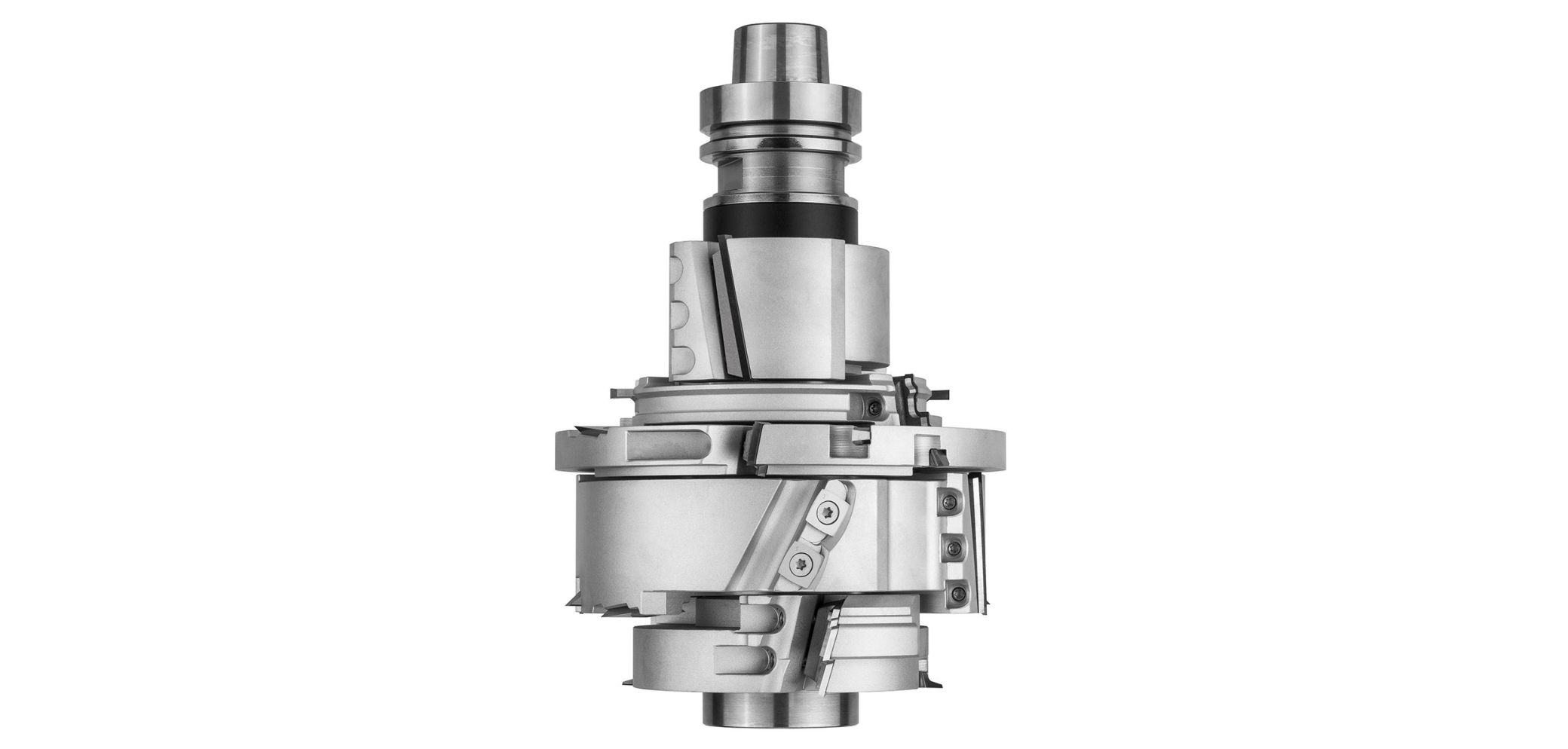
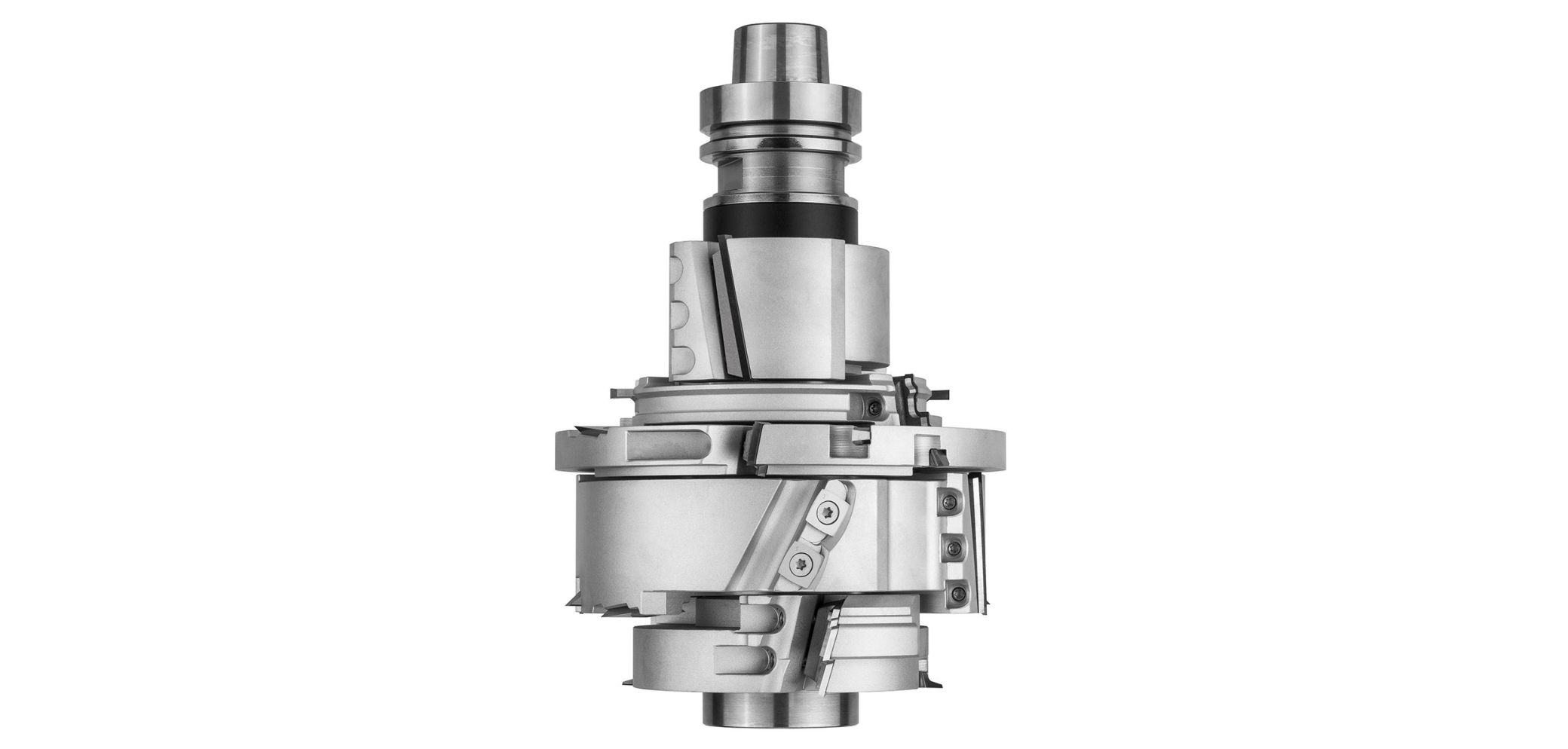
Hinter einem Fräswerkzeug wie diesem stehen oftmals viele Stunden Entwicklung. Bild: Oertli Werkzeuge AG
Hinter einem Fräswerkzeug wie diesem stehen oftmals viele Stunden Entwicklung. Bild: Oertli Werkzeuge AG
Werkzeug-Entwicklung. Egal, ob mit dem CNC-BAZ oder der Oberfräse: Für ein optimales Ergebnis ist ein gutes Fräswerkzeug unerlässlich. Dieses hat in der Regel seinen Preis. Warum dem so ist und wie viel Arbeit hinter einem neuen Fräser steckt, zeigen die folgenden Beispiele.
Einen Oberfräser für unter 5 Franken? Das ist scheinbar möglich, wenn man sich auf Seiten wie Amazon oder Ali Express verirrt. Als Fachperson fragt man sich aber zurecht, wie gut diese Werkzeuge sein können. Dank voll automatisierter Produktionsanlagen und der Fertigung in Grossserien sind die Preise für Standardfräser in den letzten Jahren laufend gesunken. Bei einem Fräser für 5 Franken kann aber kaum hochwertiges Grundmaterial verwendet worden sein, und die Qualität wird den Schreiner kaum überzeugen können, zeigt sich Martin Vogelmann, Geschäftsführer der HWS AG aus Stäfa ZH, überzeugt. «Betrachtet man nur das fertige Produkt, geht oftmals vergessen, dass selbst hinter einem vermeintlich simplen Werkzeug wie einem HW-Nutfräser schnell einmal acht Produktionsschritte stehen», sagt Vogelmann. Deshalb habe auch ein qualitativ guter Standardfräser seinen Preis.
Bewegt man sich weg vom Standard, befindet man sich schnell in anderen Preissegmenten. Für Sonderanfertigungen und Neuentwicklungen müssen Maschinen neu programmiert und eingestellt werden. Arbeitsschritte müssen möglicherweise manuell ausgeführt werden, und es braucht einen oder gar mehrere Prototypen. Je nach Gattung und Komplexität eines Werkzeuges kann die Entwicklung Monate oder sogar Jahre dauern. So brauchte das «t3»-System der Leuco AG aus St. Margrethen SG rund sechs Monate bis zur Markteinführung. Die bei Fräswerkzeugen allgemein üblichen viereckigen Wendeplatten wurden bei dem «t3»-System durch Dreieckswendeplatten ersetzt, was eine neue Ausrichtung der Achswinkel erlaubt.
Beim CNC-Werkzeugsystem «CAT» (Centrifugal Applied Technology) der Firma Oertli Werkzeuge AG aus Höri ZH vergingen gar zwei Jahre von der ersten Idee bis zur Marktreife. Für das «CAT» wurde ein neues Konzept dafür entwickelt, wie die Schneiden im Schneidensitz durch die Nutzung der Zentrifugalkraft sicher gehalten werden.
In der Serienproduktion dieser Werkzeuge sind viele Schritte automatisiert. So geschehen bei Leuco nur noch die Montage, das Wuchten und Ausmessen der Werkzeuge manuell. Auch bei Oertli laufen praktisch alle Arbeitsgänge am Werkzeugkörper automatisiert ab. Produziert wird rund um die Uhr, aber im Einschichtbetrieb. Tagsüber werden die Maschinen mit den Rohlingen befüllt, und über die Nacht erstellen die BAZ die Halbteile für die Fräswerkzeuge. Diverse Feinarbeiten, wie beispielsweise das Entfernen von Graten sowie das Auswuchten und die Endmontage, werden jedoch nach wie vor von Hand ausgeführt.
Auch im Bereich der Entwicklung ist der Mensch weiterhin unentbehrlich. So beschäftigt beispielsweise Oertli gleich fünf Personen, die dafür sorgen, dass die Werkzeuge auf dem neuesten Stand der Technik bleiben. Bei der HWS AG ist die Entwicklung hingegen meist Chefsache. Der zeitliche Aufwand für eine Neuentwicklung ist in dem Viermannbetrieb allerdings auch überschaubar. Für einen Oberfräser kann der Entwicklungszeitraum nämlich noch in Stunden oder Tagen beziffert werden.
www.hws-tools.chwww.leuco.chwww.oertli.com
«Bei einer Sonderanfertigung steht zu Beginn immer das Kundengespräch», sagt HWS-Geschäftsführer Martin Vogelmann. «Hier definieren wir die Eckdaten des Werkzeuges.» Wichtige Punkte können der Maschinentyp sein, auf dem der Fräser später zum Einsatz kommt, die Spannzangengrösse oder das zu bearbeitende Material. «Wird der Fräser später laufend verwendet, lohnt sich meist ein Wendeplattenfräser. Ist der Einsatz auftragsbezogen, empfiehlt sich ein mit Hartmetall bestücktes Werkzeug.»
Als nächster Schritt erfolgt die Konstruktion und das Erstellen der CAD-Zeichnung. Dabei richtet sich die HWS AG nach der DIN-Norm EN-847-1, welche die sicherheitstechnischen Anforderungen für Fräs- und Hobelwerkzeuge sowie Kreissägeblätter in der Holzbearbeitung definiert. Hier werden etwa die Spanlückenweiten, das Schaftdurchmesserverhältnis oder die Mindesteinspannlänge vorgegeben. «Eine Kontrollinstanz gibt es nicht. Wir fertigen den Fräser nach dieser Norm und müssen dahinterstehen können», sagt Vogelmann.
Nachdem der Kunde die Zeichnung abgesegnet hat, geht der Fräser in die Fertigung. Hier durchläuft ein HW-Profilfräser, wie er auf dem Bild oben zu sehen ist, folgende Produktionsschritte:
Der ganze Fräser wird aus dem Stahlrohling gedreht, wobei bei dem Schaft ein gewisses Zumass eingerechnet wird. Dieser Erhält seinen exakten Durchmesser erst beim Schleifen, wo auch die Schneiden ihr endgültiges Profil erhalten. Bei der HWS AG kommen sowohl handgeführte als auch CNC-Maschinen zum Einsatz. Das Auflöten der Hartmetallschneiden geschieht in reiner Handarbeit mit dem Lötkolben.
Nach dem Auswuchten wird der Schaft des Fräsers nach Norm beschriftet. Nebst den Grössenangaben, der Mindesteinspannlänge, der maximalen Drehzahl muss hier angegeben sein, ob der Fräser für den manuellen oder nur für den mechanischen Vorschub zugelassen ist. Ausserdem findet sich die Angabe zur Exzentrizität, also der verbleibenden Unwucht des Fräsers, auf dem Schaft (z. B. e = 0,06).
«Eine Sonderanfertigung im Umfang dieses HW-Profilfräsers lässt sich in der Regel in einem Arbeitstag umsetzen und würde wohl etwas um die 550 Franken kosten», sagt Vogelmann.
Am Anfang des «t3»-Systems von Leuco stand die Problemstellung «sauberes Fügefräsen». Eine Marktanalyse zeigte das Bedürfnis nach einem Fräser, mit welchem sowohl gefügt als auch gefälzt werden kann, der aber auch für spiralförmige Freiformen geeignet ist.
Zuvor habe es kein bestehendes Werkzeug auf dem Markt gegeben, welches die Kriterien optimal erfüllt, wie Bekim Izairi, Leiter Verkauf und Marketing im Innendienst bei Leuco, sagt. «Die Lösung konnte nur über eine bombierte Dreieckswendeplatte erzielt werden.» Die geometrische Form der Wendeplatten ermöglicht es, die Achswinkel so zu setzen, dass beim Fräsen ein ziehender Schnitt nach oben und nach unten erfolgt.
Die Wendeplatten seien dabei ein besonderer Knackpunkt gewesen. Diese mussten so klein wie möglich, jedoch so stabil sein, dass sie auch starken Belastungen standhalten können. Auch die Anordnung und die Positionierung der Wendeplatte am Grundkörper seien entscheidend gewesen, damit ein übergangsloses Fräsbild entsteht.
Die Entwicklungsphase des «t3»-Systems bis hin zur Markteinführung lässt sich in den folgenden Schritten zusammenfassen:
Der Entwicklungsprozess bis hin zur Markteinführung dauerte rund sechs Monate mit vielen Arbeits- und Maschinenstunden. «Würde man die gesamten Entwicklungskosten auf einen Prototyp berechnen, würde dieser wohl rund 30 000 Franken kosten», sagt Izairi.
Auslöser für die Entwicklung des «CAT Flex»-Schaftes waren die Nachfragen von Schreinern, die sich beim Profilieren auf dem CNC-BAZ höhere Produktivität wünschten. Als Schaftwerkzeug mit kleinem Durchmesser erlaubt der «CAT Flex»-Schaft höhere Drehzahlen und somit auch höhere Schnittgeschwindigkeiten.
«Bei einer klassischen Neuentwicklung folgen wir einem fest definierten Prozess», sagt Zoran Ostojic, Entwickler bei der Oertli Werkzeuge AG. Dieser Prozess lässt sich in vier Phasen gliedern:
Ein grosses Entwicklungsprojekt kann mehrere Hundert Arbeitsstunden umfassen. «Als Gegenwert würde man dafür problemlos einen schnellen Sportwagen bekommen», sagt Ostojic. Der «CAT Flex»-Schaft benötigte allerdings nur noch ein Drittel der zwei Jahre Entwicklungszeit, die das Grundkonzept des «CAT»-Systems benötigte. «Bei einer Weiterentwicklung sind gewisse Parameter schon bekannt, und fertig entwickelte Baugruppen können zusammengesetzt werden. Somit lässt sich viel Zeit einsparen», sagt Ostojic. Technische Sackgassen kennt das Entwicklerteam von Oertli nicht. «Unser Motto ist: Jedes technische Problem ist lösbar. Vielmehr ist die Herausforderung oftmals, die Problemstellung wirtschaftlich zu lösen», sagt Ostojic. «Man wolle kein Over-Engineering betreiben, sondern nur genau das entwickeln, was es braucht.»
Veröffentlichung: 11. April 2024 / Ausgabe 15/2024
Tischkreissägen. Damit wiederholbare, genaue Schrägschnitte gemacht werden können, gibt es auf dem Markt viele technische Hilfsmittel. Das reicht von der raffinierten Mechanik bis zur weitgehenden Automatisierung. Damit entfallen dann so manche lästigen Schritte von früher.
mehrHandwerkzeug. Die Anzahl an Schweizer Produzenten von Handwerkzeug für Schreiner ist überschaubar. Die Werkzeughersteller haben ihren besonderen Platz gefunden, was ohne eine weltweite Vermarktung der Produkte kaum möglich wäre.
mehrPaidPost. Die neue «Stream B MDS 2.0» von Biesse ermöglicht mit ihrer neuen Kantenanleimtechnologie flexible Losgrösse-1 Produktion und maximaler Leistungsfähigkeit mit bis zu 1'200 Platten pro Schicht.
mehr